三宇集团:业内首台钢铝阻焊机器人
转载自合肥晚报
原文链接 http://www.hf365.com/2022/0803/1418566.shtml
机械手臂灵活地上下翻飞,伴随着“咔嚓”一声,用时不足一秒钟,一小块钢板就和一块铝板就被牢牢地焊接在一起。
将钢和铝两种“秉性”不同的材料牢固地“缝纫”在一起绝非易事。经过多年的技术研发,三宇集团陆续攻克异种金属点焊连接、多层板点焊连接等技术难题,并推出了业内首个钢铝阻焊设备——三宇阻焊机器人。
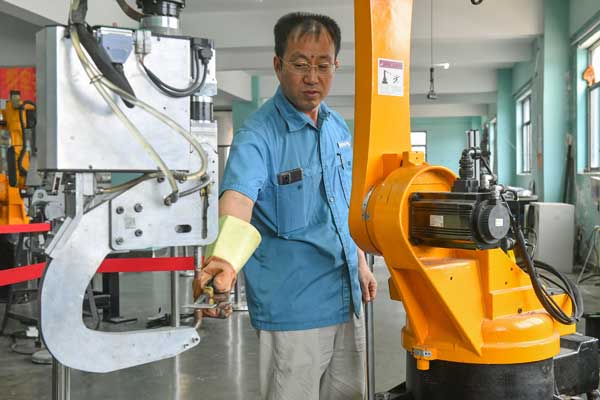
潜心研发
挑战钢铝焊接难题
在汽车界,钢铝混合车身一直是“豪华”的象征。
作为现代工业中用途广泛的两种材料,钢材和铝合金各有所长,也各有其短:钢材坚韧却比较笨重;铝合金轻巧、耐腐蚀却不够刚强。钢铝混合车身,则能吸取两种材料的优点,发挥取长补短的“功效”,让汽车兼具安全性和轻量化的优势。
由于两种材料“秉性”不同,要将他们完美地“结合”在一起极为困难。钢的熔点是1550℃,铝的熔点仅为600℃左右,若使用传统焊接让他们“手拉手”,在钢达到焊接温度时,铝早以融化。
“传统焊接方式行不通,国外相关企业便研发出钢铝铆接技术。目前,这一技术也只应用在少数豪华汽车品牌上。”三宇集团董事长袁忠杰介绍,“就我国汽车制造业而言, 铆接工艺所需设备基本依赖进口, 连铆钉也不例外。此外,铆接工艺因为难度大,生产成本高,效率也比较低。”
袁忠杰,1982年毕业于安徽大学物理学专业,毕业后曾在一家省属科研机构担任技术攻关带头人,后下海创业。1989年,他牵头创办合肥三宇电器技术研究所。
30多年来,袁忠杰的团队一直在从事焊接和智能化生产领域的研究,尤其专注于汽车智能化焊接技术研究。2000年,他曾和科大讯飞刘庆峰等一起当选合肥市第三批专业技术拔尖人才。
“多年的焊接行业的经验和物理学背景告诉我,这事虽然难度大,但却是可行的!”袁忠杰所说的,正是他带领团队经过数年研发的钢铝“异种金属”电阻焊技术。
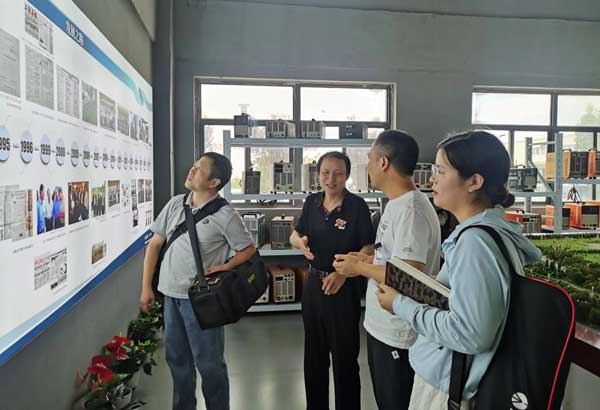
优势明显
钢铝“缝纫”助力轻量化
在三宇集团研发车间,袁忠杰和团队向记者现场演示了这一技术的应用。
车间里,摆放着企业打造的业内首个钢铝阻焊设备——三宇阻焊机器人。工作人员将一小块钢板就和一块铝板放在工作区域,机器人机械手臂灵活地上下翻飞,迅速定位焊接点。
伴随着“咔嚓”一声,用时不足半秒,两块板就被牢牢地焊接在一起,表面仅有一个直径不足一厘米的焊点。
焊接后的钢铝板材牢固程度如何?工作人员随后将它送上专业的设备进行拉伸剪切试验结果显示,测试设备施加5944牛的力才将两块板材给分离开。换算成重量单位来看,这个焊点可以承受近600公斤的力量。
袁忠杰介绍,铆接技术单点可承受的拉力仅为三四千牛(换算成重量单位约为二三百公斤),除了强度的提升,钢铝阻焊技术还有明显的成本和生产效率方面的优势。“每个焊接点的成本由铆接的1至2元,降至几分钱。”更重要的是适用于轻量化车身的高强度钢,强度达到1500兆帕以上,但由于技术局限性无法用现有铆接技术连接。
“锻、铸、铆、焊是金属加工、连接的必要手段、尤以‘焊接’效率最高、成本最低,所以是加工手段的首选。在工业化最发达的美国,焊接被视为制造业的命脉。”袁忠杰介绍,与以往不同的是,如今,焊接已经从一种传统的热加工技艺发展到了集材料、冶金、结构、力学、电子等多门类为一体的综合性学科。而钢铝阻焊技术的关键在于复杂的波形控制和对电流电压的精确掌握。
在“双碳”背景下,汽车轻量化意味着更少的能耗。袁忠杰认为,钢铝混合车身是汽车轻量化的必由之路。钢铝阻焊技术除了在汽车制造领域,在航空、航天领域也具有极大的应用前景。
(见习记者 王雅雯 合报全媒体记者 李后祥 袁兵 )